Introduction
Accessafe ha ricevuto l’incarico di sviluppare un progetto di adeguamento sicurezze di una macchina testa verniciante, messa a disposizione dall’azienda ordinante ai lavoratori presso lo stabilimento prima dell’entrata in vigore del DPR 459/96 e perciò sprovvista di marcatore CE.
On the basis of the on-site evaluation and the information provided by the operators who worked on the plant, it was determined that the Machines needed to conform with the minimum requirements of annexe 5 of the Italian Legislative Decree 81/08. The upgrade makes the machine meet the requirements of the directive: ATEX 2014/34, the Machinery Directive 42/2006 and conformite to the harmonised standards listed below:
- EN 12100: 2010 Machinery Safety
- EN ISO 13857: 2008 Safety distance for upper and lower limbs
- EN 349: 2008 Minimum gaps to avoid crushing hazards
- EN ISO13850: 2015 Emergency stops
- EN 14119: 2013Interlocking devices connected to the guards
- EN 14120: 2015 Fixed and movable guards
- EN 1037: 2008 Prevention of unexpected start-up
- EN 547: 2009-1 Human body measurements: whole body access openings
- EN 547: 2009-2 Human body measurements– limb access openings
- EN 547: 2009-3 Human body measurements – anthropometric data
- EN ISO 14738: 2009 – Anthropometric requirements for work stations
- EN 60204-1:2006 – Machine Electrical equipment
- EN 61439-1:2012 Low voltage electric cabinets- General rules
- EN 13849-1: 2016 Safety-related parts of control systems
Project development
The project design included the use of panels with vertical aluminium profiled frames and galvanised mesh suitable for the machine hazard zones as per EN ISO 1357:2008 as an infill.
The profiles used for the project have the following dimensions:: 32X32 – 32X45 – 18.5 X32 – 18.5X45 – 45X45 – 32X45, and have been built in conformance with the pertinent standard requirements of EN 14120:2015.
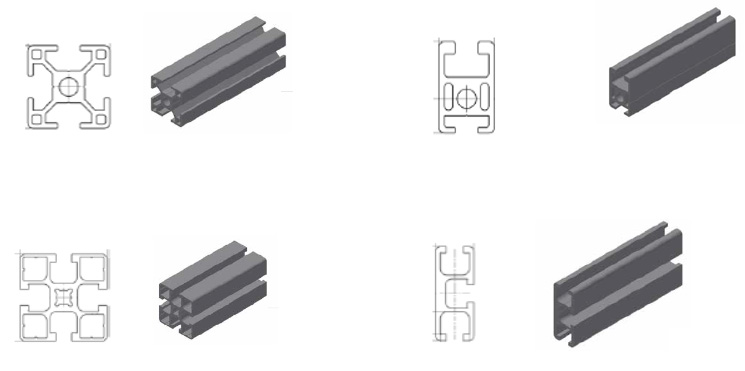
We have selected Euchner ATEX certified position sensors, here below the list of specific models: CES ( 1-2-3-4-7-8-9-10-11-12 ) and pedestrian access points behind the CET (5- 6) as in the illustration below:
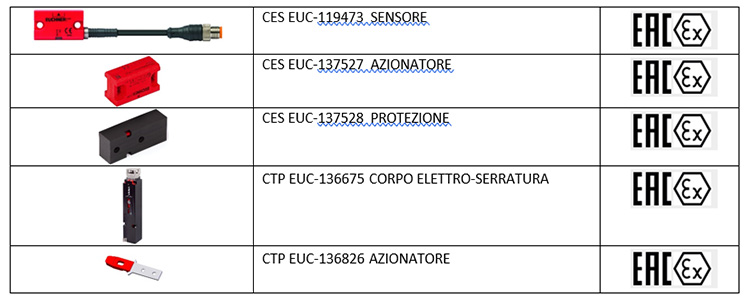
The previous mentioned components were positioned as follows:
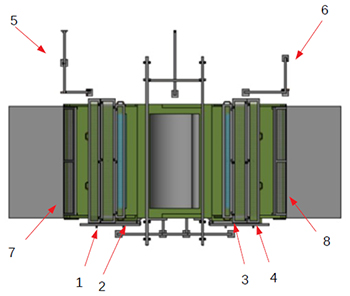
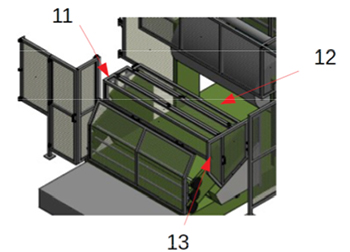
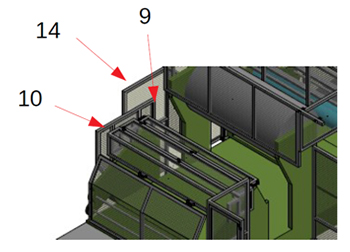
Working conditions
The machine is equipped with two work groups called A and B, what follows is the safety elements function mode for both coating heads analysed.
When group A-B are running, the safety logic will follow the conditions below:
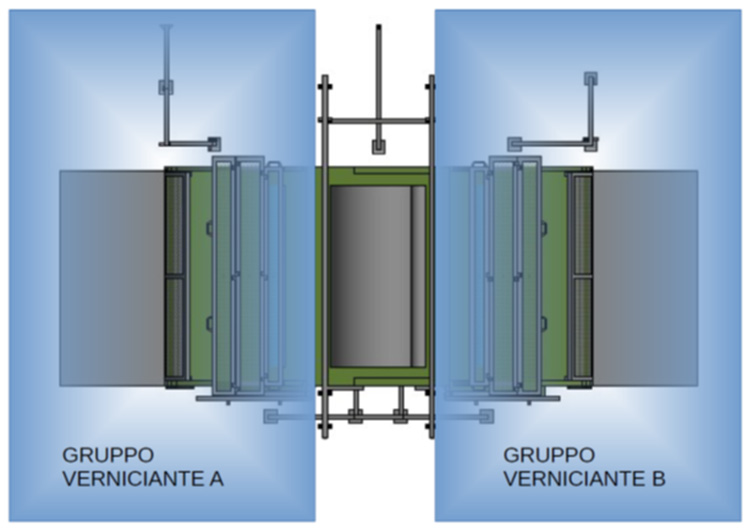
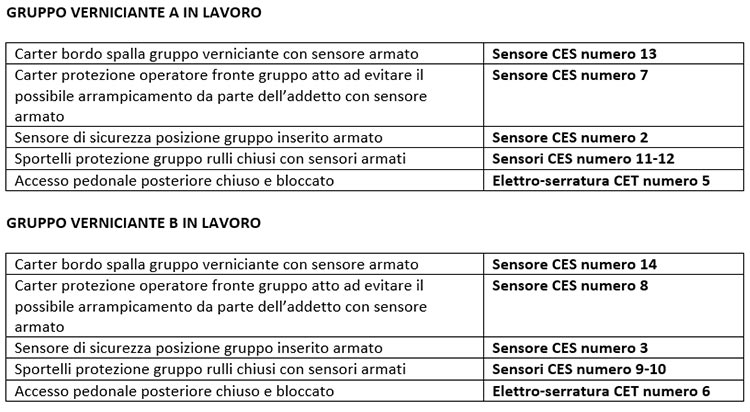
Please note that in absence of the above listed conditions, the machine cannot run.
MAINTENANCE PROCEDURES ONCE UPGRADE HAS BEEN COMPLETED
In caso di esigenza di ingresso tramite la porta posteriore Accessafe ha previsto una pulsantiera con selettore a chiave ad attivazione del pulsante di richiesta accesso. Una volta attivato e premuto il pulsante di richiesta, invierà una richiesta di arresto del gruppo interessato, il quale alla fermata abiliterà tensione alla bobina di sblocco accesso consentendo l’ingresso all’operatore in condizione sicura. In caso di manutenzione verrà fornito uncomando di estrazione della testa verniciante interessata, il quale fermerà il ciclo macchina disarmando il sensore (sensore 2 per gruppo A – sensore 3 per gruppo B) inibendo ogni possibile movimento
Once the extraction has been completed a safety sensor will be activated in “REST” position (called N1 for group A and N4 fro group B).
Once this procedure has been completed the extracted head cannot be activated and it will be possible to remove and open the protection housing to reach parts object of the maintenance operations. The second head is still in place and can work in the conditions of armoured sensors, as previously described, thanks to the protection housings put in place which will prevent the maintenance operator from reaching moving parts.
At the end of the maintenance intervention, all the fixed guards shall be put back into place and the movable guards shall be closed, such operation is assured by positioning and activating the safety sensors. If such operations have not been carried out, it will be impossible to reset or move in any way the serviced coating head. If all conditions above have been met, it is possible to reset safety sensors using the blue light push button which will emit a signal to warn the machine is restarting.
When the button is pressed a ray of continuous light will light the area and it will be possible to give the move into group position command by activating the safety sensor and starting the machine work cycle.
Accessafe ha previsto due pulsanti di emergenza a fungo in prossimità dell’area di stazionamento operatore di testa ai due gruppi di verniciatura.
Further analysis by Marco Vaccarone
CMSE® Certified Machinery Safety Expert
In this case we were faced with the securing of a Pick and Place manipulator with a vacuum picking organ performing at low speed, due to the fragility of the product, so lower than 250 mm/sec. and 5 pieces/ hour.
This allowed us to manage product haul-off opening as a residual risk by affixing dedicated warning signs (Directive 92/58/CEE) which inform about the possible hazard should the operator mounts on the conveyor belt. By doing so we have achieved a safety solution which does not require the use of photoelectric barriers.