Accessafe ha ricevuto l’incarico dalla Carcano Antonio SPA di sviluppare il progetto di messa in sicurezza di una nuova parte di impianto considerando anche quello già esistente.
L’analisi rischi e la relativa specifica sviluppata dal costruttore della parte di nuova fornitura è stata consegnata ai tecnici Accessafe per lo sviluppo del layout con i relativi controlli sugli accessi rispettando il PLr (secondo UNI EN ISO 13849:2016).
Risk analysis and the new plant manufacturer’s technical specifications were passed on to Access’s engineers for the lay-out design with pertinent access control which respected PLr (as per UNI EN ISO 13849:2016).
Indeed, the company’s production process is entirely integrated and traceable from raw materials to end-product as required by GMP, UNI EN ISO 9001:2008 and UNI EN ISO 14001:04 standards: an example of quality and efficiency to assure customer satisfaction and environment protection.
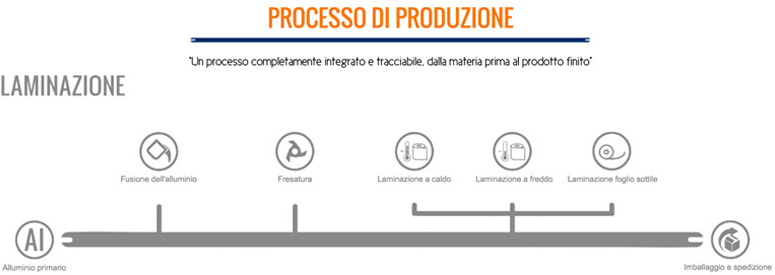
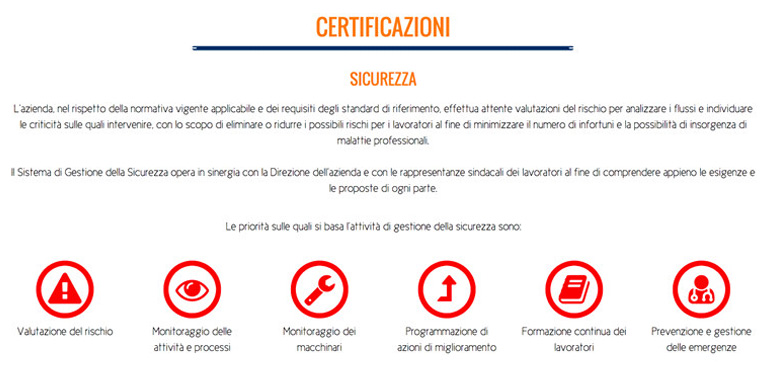
Il layout riguardante le protezioni è stato sviluppato da Accessafe secondo Direttiva Macchine 42/2006 e relative normative applicabili, seguendo il sistema di Sicurezza Funzionale Perimetra per la messa in sicurezza chiavi in mano dell’impianto.
The order, which consisted of both the supply and mounting of the mechanical part and the supply of material, installation and cabling to the plant, was processed along with the scheduling of mechanic and electric technical staff intervention for a total of 8 working days from the material delivery date and for a total of three weeks from project acceptance.
Functional tests were carried out at the end of set-up in the presence of the plant manufacturer and Carcano technicians, followed by the handing over of all documentation relative to certifications, instruction and maintenance manuals and technical data sheets.
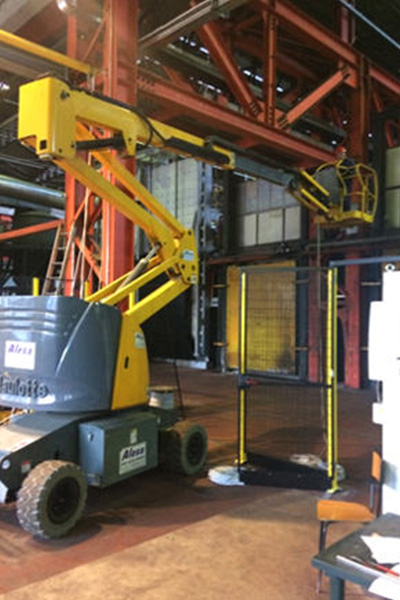
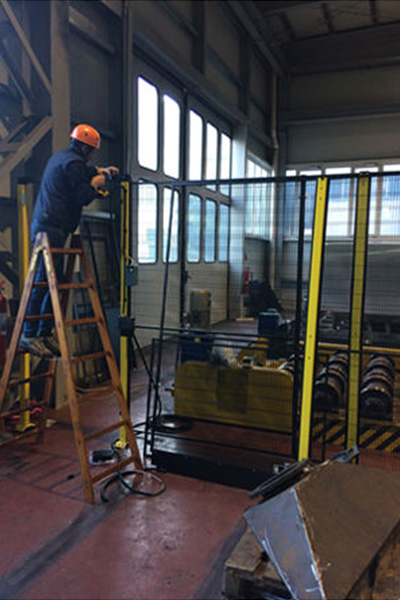
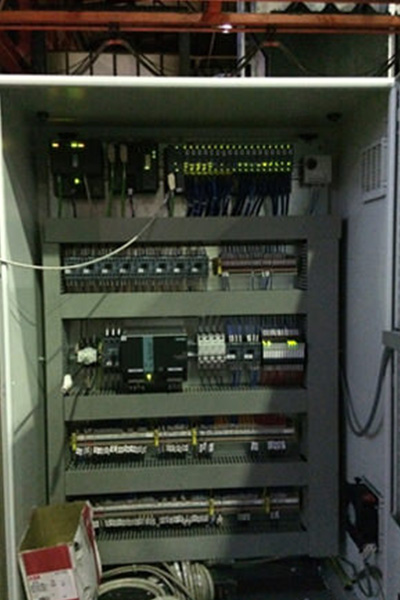
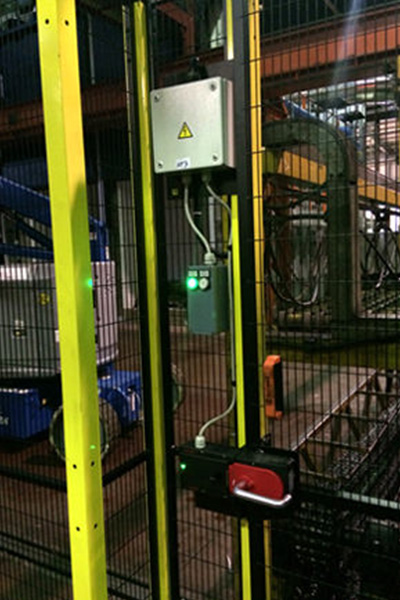
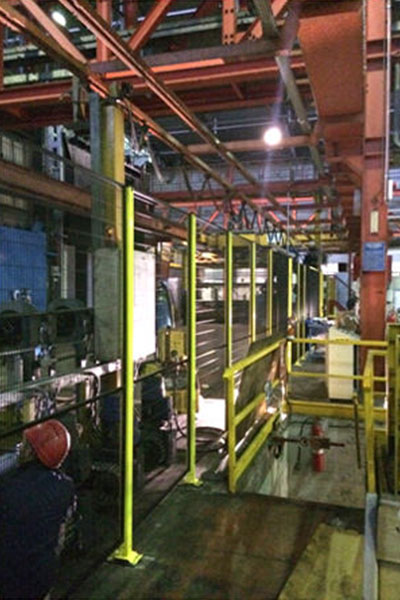
The executive project Functional Safety
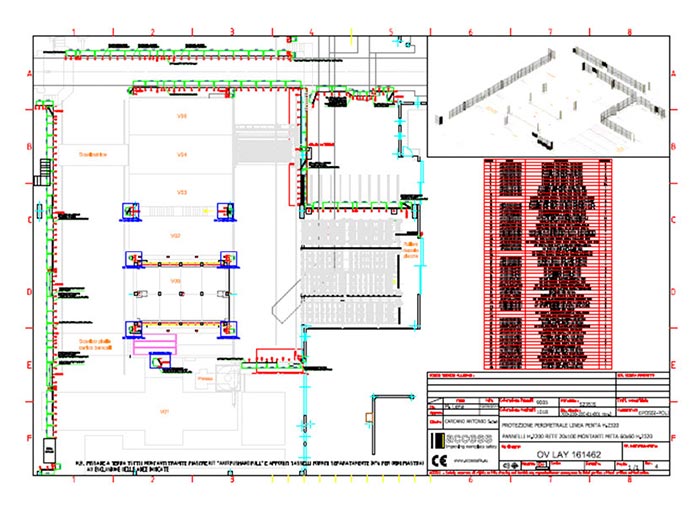
Il progetto esecutivo Sicurezza Funzionale Perimetra è stato sviluppato secondo lo schema a blocchi caratteristico di questo servizio innovativo di Accessafe, a disposizione dei clienti anche in maniera parziale: Acquisizione e verifica analisi rischi e RES, Progettazione esecutiva del sistema di protezione perimetrale, Fornitura dei componenti meccanici ed elettronici, Installazione e cablaggio, Test funzionali, Formazione, Rilascio documentazione tecnica, Assistenza programmata post vendita.
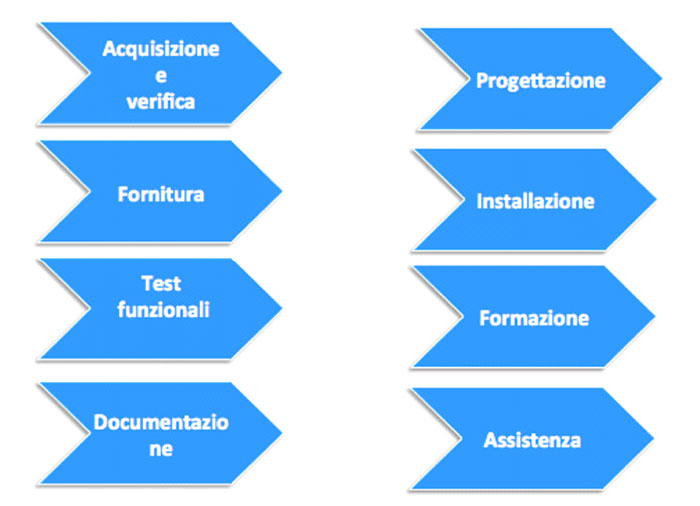
Regulatory insight from Marco Vaccarone CMSE® Certified Machinery Safety Expert Functional Safety Manager
During the review of the specifications resulting from the manufacturer’s risk analysis delivered to us for the evaluation and development of the securing project, I was able to collaborate with the engineers who had developed it because there was a risk consideration to the achievement of PLr that could have subjected the related certification to litigation. The required PL was equal to „d,“ and to achieve it, an electro-lock with a latch system for mechanical failure exclusion was planned: guaranteeing this performance would have resulted in the manufacturer having to demonstrate that it had complied with the failure exclusion requirements of UNI EN ISO 13849-2:2013 (Table A.4) and that the maximum actuator engagement speed required by the device manufacturer would not be exceeded under any circumstances.
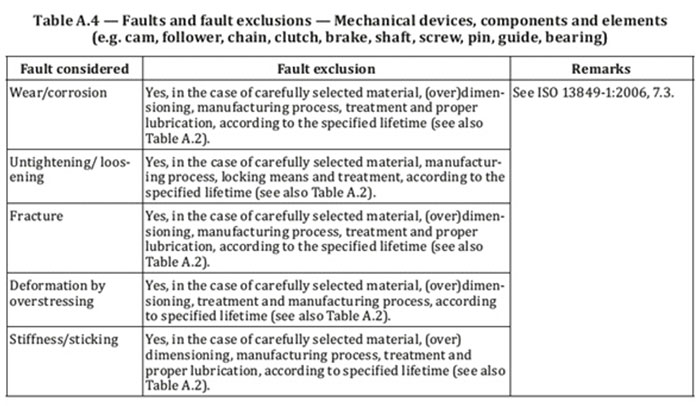
In view of this consideration, it was decided to modify the design by applying electro locks and sensors with transponder technology to ensure the achievement of PLr without fault exclusion.