
Risk assessment is a fundamental requirement for achieving machine and plant safety and ensuring compliance with current regulations throughout the lifecycle: from design and manufacturing to commissioning and decommissioning.
Accessafe offers a complete risk assessment service following specific directives and standards:
- For CE-marked machinery, the assessment is performed according to the essential safety and health requirements of the Machinery Directive 2006/42/EC and the new EU Machinery Regulation 2023/1230.
- For machines or plants in use that were put on the market before September 1996, the risk assessment is performed according to the minimum safety requirements of Legislative Decree 81/08.
In both cases, the risk assessment is carried out using the standard EN ISO 12100:2010 Machinery safety – General principles of design – Risk assessment and risk reduction. The methodology used allows for the identification of hazards to reduce associated risks, ensuring a safe working environment that complies with current regulations, regardless of the age of the machinery or the system in use.
Methodology Used for the Risk Assessment Process
We follow a comprehensive and structured approach to analyze and reduce risks related to the use of machinery throughout its lifecycle:
- Verification of Applicable Standards
- We verify the applicable standards for assessing the machinery or system of machines.
- Application of the Iterative Risk Assessment Method
The iterative method is represented in the following flowchart:
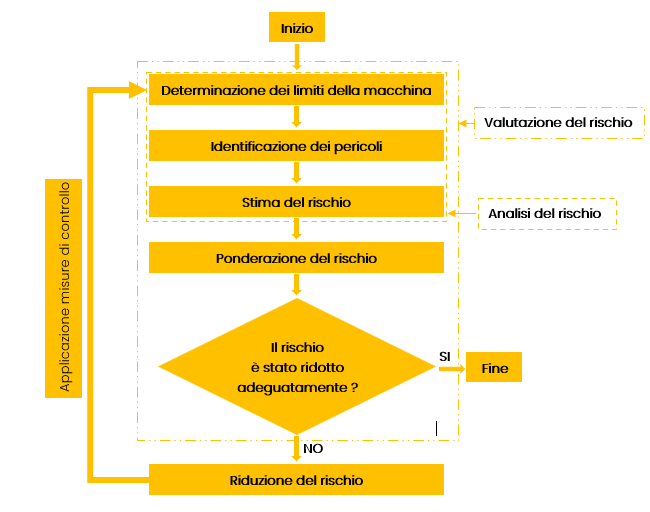
The assessment is carried out according to the following steps:
-
Determination of Machine Boundaries
This includes the intended use and reasonably foreseeable misuse. -
Hazard Identification
We identify potential hazards arising from the use of the machine under all foreseeable operating conditions. -
Risk Estimation and Rating using HRN (Hazard Rating Number) Method
We assign a risk value (HRN) based on parameters such as: severity of damage and likelihood of occurrence. Specifically, the method uses the following factors: Probability of occurrence (PE), Frequency of exposure (FE), Maximum probable injury (MPL), Number of persons exposed (NP)
HRN = PE x FE x MPL x NP -
Preparation of the Evaluation Report
We document the results of the risk assessment on our report template, considering both acceptable and unacceptable risks, and proposing possible solutions (Safety Concept) for mitigating these risks, applying harmonized standards and specific regulations. -
Action Plan for Risk Reduction
If necessary, we develop an action plan to reduce risk and make adjustments to the machinery: we propose solutions that comply with European directives and regulations or other applicable international standards based on the machine’s intended use, utilizing harmonized standards or specific technical regulations.
Advantages:
- Ensure the safe use of machinery, reducing potential accidents.
- Guarantee full productivity of machinery.
- Ensure compliance with current directives and regulations.
- Ensure a longer lifespan for machinery by identifying safety issues in advance.
- Optimize safety-related costs by avoiding late corrective interventions.
WE FOLLOW ALL STAGES OF THE PROJECT FROM RISK ANALYSIS TO SAFE PLANT COMMISSIONING.

DUE DILIGENCE MACHINERY PARK

RISK ASSESSMENT

SAFETY DESIGN

SAFETY COMPLIANCE

SAFETY FUNCTION VALIDATION

CE MARKING

DUE DILIGENCE MACHINERY PARK

RISK ASSESSMENT

SAFETY DESIGN

SAFETY COMPLIANCE

SAFETY FUNCTION VALIDATION
